Depuis quelques années, nous assistons à un véritable bouleversement des entreprises.
Désormais les Supply Chains ne sont plus constituées en chaîne mais en vastes réseaux d’acteurs, les cycles de vie produit raccourcissent, les clients veulent des délais de plus en plus courts, les produits sont plus variés et customisés et les durées d’approvisionnement peuvent être longues notamment à cause de la mondialisation.
Cependant face à ces changements la plupart des entreprises continuent d’utiliser le MRP (Material Requirement Planning) comme système de planification central. Ce modèle, commercialisé dans les années 70, était parfaitement adapté à un contexte où la demande était supérieure à l’offre mais ne répond plus aux défis actuels et se heurte à de nombreuses difficultés : retards de livraison, ruptures de stocks, lead times longs, mode pompier, prévisions peu fiables, etc.
Il est donc temps de trouver un nouveau modèle et la méthode Demand Driven Material Requirements Planning ou DD MRP semble être une réponse adaptée aux défis de la “Nouvelle Normalité ».
Poursuivez la lecture pour en savoir plus !
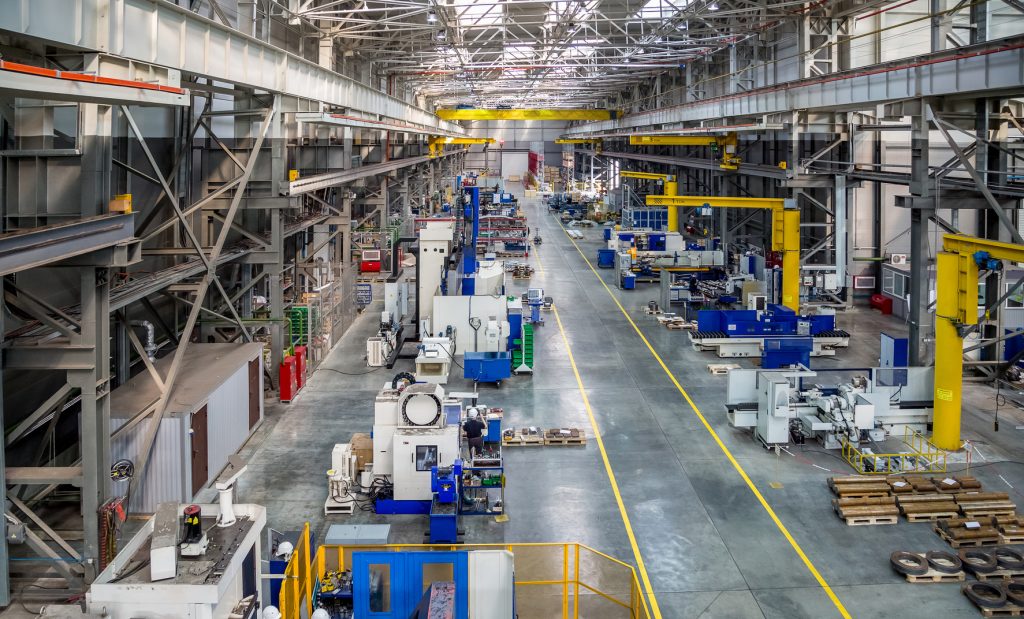
Qu’est-ce que le DD MRP ?
DD MRP signifie Demand Driven Material Requirements Planning ou planification des besoins matériels selon la demande en français. Il s’agit d’une méthodologie de planification de production, née dans les années 2000 aux Etats-Unis par Carol Ptak et Chad Smith, reposant sur la demande réelle des clients. On parle désormais de flux tirés par la demande, et non plus poussés par la production.
Grâce au concept de buffers et de positionnement de stocks stratégiques (matières premières, composants et produits finis), la méthode DD MRP permet de déterminer les quantités à approvisionner afin d’avoir un niveau de stock toujours au plus juste, baissant ainsi les coûts de stockage, les ruptures de production et augmentant la satisfaction client.
Reposant sur différents concepts issus du MRP (Material Requirement Planning), DRP (Distribution Requirement Planning), Lean, 6 Sigma, et de la théorie des contraintes mais en y ajoutant des innovations spécifiques, le DD MRP permet de résoudre les conflits entre les différentes approches avec des résultats rapides.
Ainsi, la méthode s’est naturellement imposée en premier lieu dans l’industrie puis a progressivement touché la distribution ainsi que les PME. Cependant de nombreuses grandes entreprises et multinationales ont également commencé à voir le potentiel de DDMRP telles que : MICHELIN, ACESCO, COCA COLA, SHELL, BIOMERIEUX, etc.
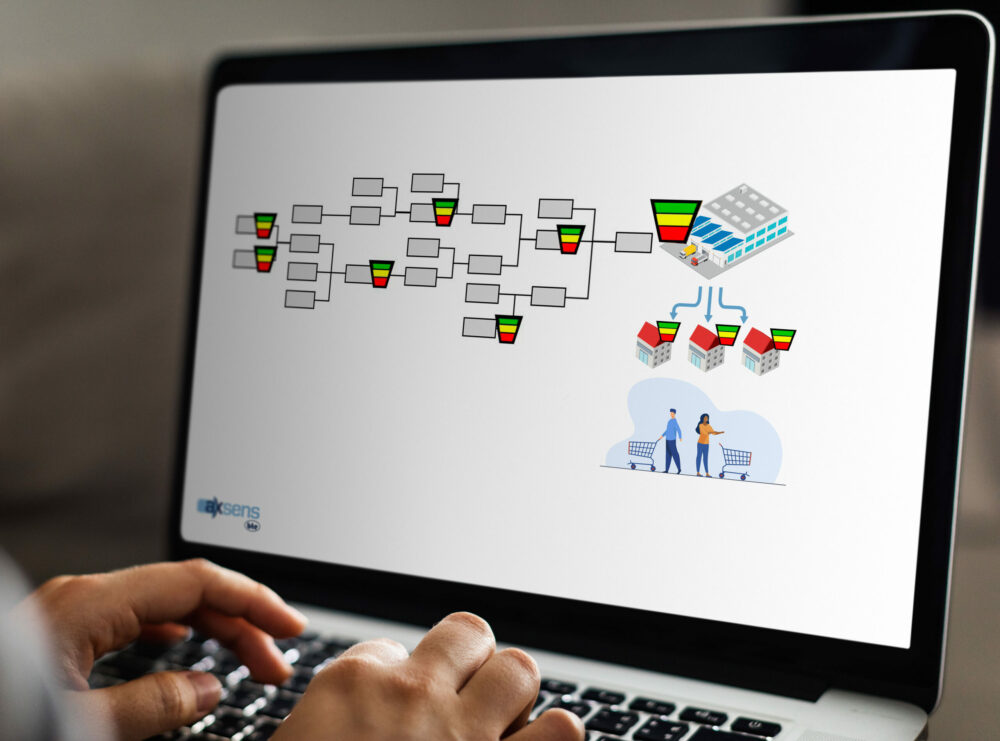
Comment mettre en place le DDMRP ?
La mise en place de la méthodologie DD MRP dans une entreprise est très simple et peu coûteuse. Elle se met en œuvre en 5 étapes et créé un système agile qui protège et accélère les flux.
Le pilotage des opérations est collaboratif et intuitif :
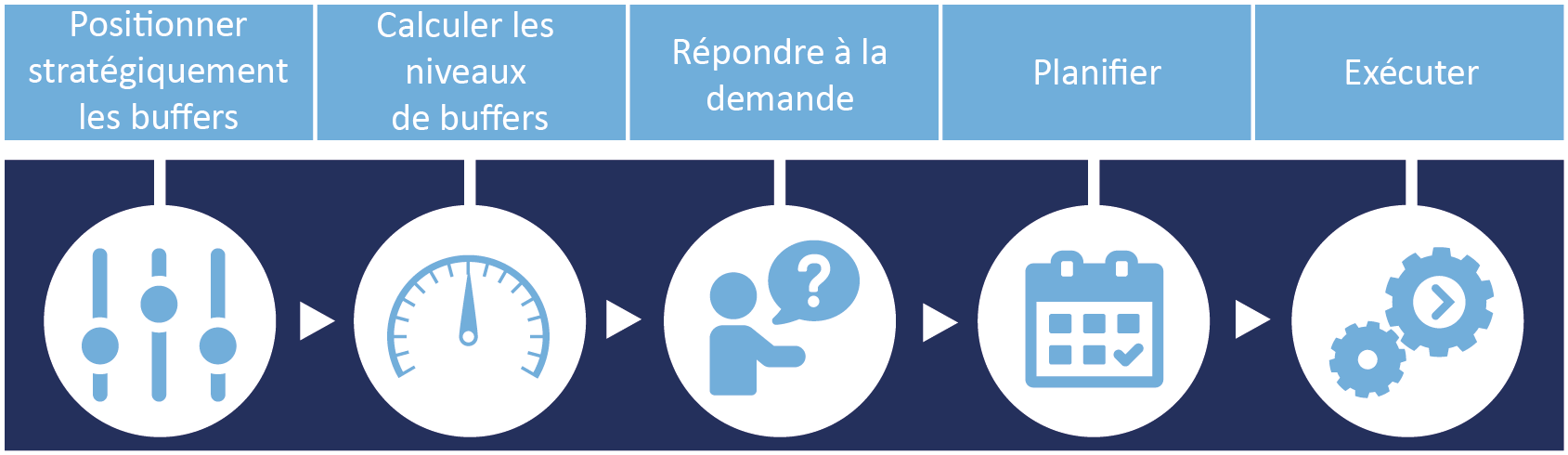
1. Positionner stratégiquement les buffers
Afin de compresser les délais et de réduire les effets coup de fouet, DD MRP développe un concept important, celui de « découplage ». Il s’agit là de positionner différents buffers (tampons) tout au long de la chaine logistique afin de créer intelligemment des stocks dans le but de découpler la demande du client et la production.
2. Calculer les niveaux de buffers
Définir les tailles des buffers pour que le niveau des stocks soit en adéquation avec la réalité de la demande. Les buffers sont divisés en 3 zones : verte, jaune et rouge.
• La zone verte permet de déterminer le nombre de commande / OF et leur périodicité
• La zone jaune : elle permet de définir les seuils de commande. Elle dépend du délai d’approvisionnement et de la CMJ (consommation moyenne journalière)
• La zone rouge : zone de sécurité calculée en fonction de la CMJ (consommation moyenne journalière), du délai d’approvisionnement et de la variabilité

3. Répondre à la demande
Pour répondre au plus juste à la demande (saisonnalité, nouveauté, fin de vie, etc.), il faut rendre les buffers « dynamiques », c’est-à-dire redéfinir régulièrement leurs tailles.
4. Planifier
Générer des ordres de réapprovisionnement et fabrication lorsqu’un seuil critique est franchi en anticipant les niveaux de stocks futurs en fonction des stocks actuels, commandes à satisfaire, etc.
5. Exécuter
Commander et produire en fonction de la disponibilité des articles. La définition des priorités est facilitée et la collaboration encouragée grâce notamment au management visuel. DDMRP favorise le travail d’amélioration continue.
Axsens BTE est partenaire du Demand Driven Institute depuis le lancement de la méthode DD MRP en France en 2013. Notre cabinet vous propose la mise en place d’outils simples pour simuler l’impact de la méthode sur vos stocks et les taux de services.